How do Adhesives Accelerate the Development of Miniaturised Electronic Devices?
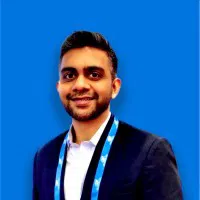
Utsav Shah is a 34-year-old entrepreneur with a passion for scientific discovery. Utsav’s journey began with a deep dive into materials science, earning degrees from USC and the Institute of Chemical Technology. He’s the visionary founder of Kohesi Bond, a top-rated adhesive manufacturer, and Cenerge Engineering Solutions, a leader in heat exchangers and cryogenic pumps. With over a decade of experience, Utsav consults across various industries, ensuring they have the perfect adhesive solution for their needs. Connect with him on LinkedIn!
Recent Blogs
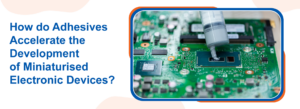
How do Adhesives Accelerate the Development of Miniaturised Electronic Devices?
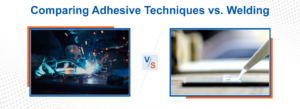
Comparing Adhesive Techniques vs. Welding
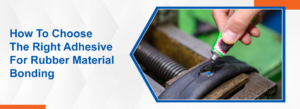
How To Choose The Right Adhesive For Rubber Material Bonding
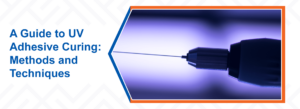